4 essential design features of rubber products
Posted on 12/05/2019 Category: Product & Application News, Rubber gaskets, Rubber Industry News, Rubber moulding, Rubber sheeting
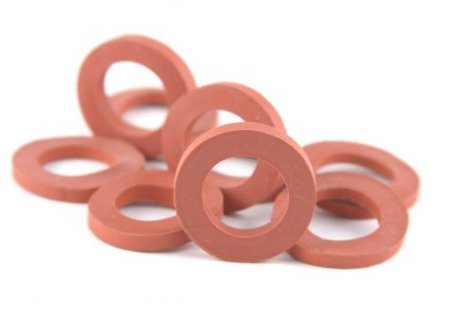
When it comes to designing the ideal rubber part for the rigours of specialist applications, there are several rubber product design features worth bearing in mind. Here, Martin’s Rubber outlines our four-part rubber product design guidelines for attaining the optimal solution each and every time.
1. Rubber tolerance
All elastomers undergo a certain degree of shrinkage. This depends on the material, of course, but also a range of other factors, including but not limited to: tool design, moulding method, geometry of the part, and hardness of the compound. With so many variables to consider, expert advice can often make life easier. Our experienced technical staff at Martin’s Rubber are always ready to provide guidance and support to ensure you attain the correct tolerance for your product or part.
We strongly recommend that designers consult with our technical team about tolerances at the earliest possible stage. Establishing these parameters early on will ensure that the most appropriate solution can be developed for your particular application requirements. Our experts employ cutting edge technology, including non-contact profile projectors (shadowgraphs), to guarantee optimal tolerance levels.
2. Chemical compatibility
No rubber material is perfect. As such, it is largely a case of understanding the application and matching the most suitable material to the environment in which it will operate. The growing array of polymers and manufacturing processes available for rubber products has increased the range of solutions to any given problem. Martin’s Rubber has a wealth of specialist rubber experience that we can draw upon to provide advice on the most appropriate rubber product design features.
One of the major challenges facing manufacturers today is the safe handling and processing of chemical substances. With that said, selecting the most appropriate elastomeric material capable of withstanding these typically aggressive and corrosive types of media is essential. We offer a range of chemical resistant materials – such as EPDM, Viton®, Aflas® and Perfluoroelastomer (FFKM) – and our technical experts are only too happy to support you during your selection process.
3. Shore hardness
Shore hardness scales were developed to provide a common reference point for comparing different materials. This is measured using a durometer gauge, which employs a spring-loaded steel rod to compress the surface of the sample material and then return a reading. A shore hardness of 0 equates to the maximum amount of indentation possible, while a shore hardness of 100 is indicative of an extremely high resistance to indentation.
Shore hardness also provides a measure of flexibility or stiffness, known as flexural modulus. This indicates a rubber material’s resistance to bending. Hardness and flexural modulus are interdependent because as hardness increases, so does flexural modulus. On the flip side, the hardness of a material may be inversely proportional to its coefficient of friction. For example, softer thermoplastic elastomers usually contain more oil, which generally results in higher surface tack.
4. Geometry
The manufacturing process prescribes some limitations to how your final product will look. The combination of rubber’s viscoelastic properties and traditional moulding techniques therefore demand a certain degree of design awareness. The simpler and more symmetrical the geometry of your design, the easier it will be to produce. It is worth bearing in mind that complicated geometries can often require additional finishing techniques, like trimming, deburring and hollowing.
Inevitably, these processes could well increase the cost of your final part. The variability of the end result could also increase the risk of part rejections. As you can see then, simpler designs offer numerous advantages, not least in terms of quality, reproducibility and cost. As ever, our experts can provide invaluable help and guidance at the design stages to make the final manufacturing process as smooth as possible.
Speak to Martin’s Rubber today
At Martin’s Rubber, we offer a full consultation service and are more than happy to visit customer sites to look at specific problems or work programmes. Seeking the assistance of an expert at the earliest opportunity will ensure you gain the relevant rubber product design features you need. This in turn can avoid any wasted time and money in the long run. Our experts are on hand to help in terms of application requirements and material selection, helping you to choose the correct rubber product design features and tolerance band.
To find out more about our design consultation services, or to discuss your specific application requirements in more detail, please contact Martin’s Rubber on +44 (0) 23 8022 6330 or email [email protected].