A guide to Martin’s Rubber’s rubber moulding techniques
Posted on 08/09/2017 Category: Rubber moulding
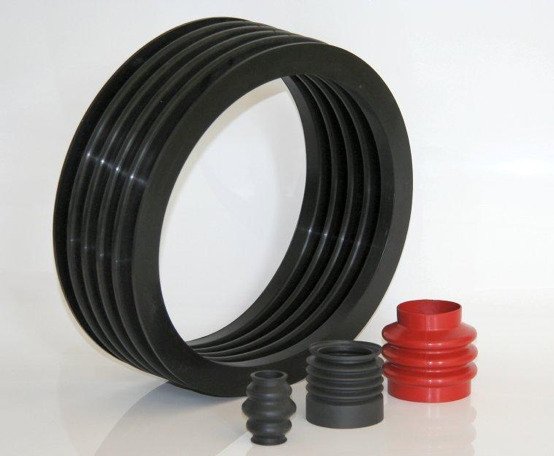
In our latest blog, we give you a detailed overview of the main rubber moulding techniques that we employ here at Martin’s Rubber. As such, we will explore the process of injection moulding and explain the intricacies of compression and transfer moulding techniques.
The process of injection moulding
The process of injection moulding forces a precise amount of rubber from a tube or cylinder into a closed, heated mould. We have a wide selection of injection moulding machines, with up to 1litre capacity and a clamp force of 220 tonnes. Injection moulding can be used for rubber or plastic. The only difference being that rubber is heated whilst being injected and requires more pressure.
The benefits of injection moulding rubber include:
● It is cost-effective for higher quantities.
● It produces very little waste on long runs.
● The manufactured parts may not require trimming work.
● It produces consistent and accurate goods.
● Cycle times can be quicker than other techniques.
● Tight dimensional tolerances can be achieved.
● Low flash levels.
● Ideal for large volumes of small to medium parts.
What is transfer moulding?
Transfer moulding provides the accuracy and consistency of injection moulding, however it is more likely to be used for shorter runs and therefore avoids the potential costs associated with full injection tooling. The process begins with the raw materials being prepared as ‘pre-forms’ that are then loaded into a pot internal to the mould tool. An integral plunger then compresses the rubber in the pot, so that it is forced through holes or sprues into the product cavity to fill it in like an injection machine would.
The benefits of transfer moulding include:
● More consistent and accurate than compression moulding.
● Tighter dimensional tolerances.
● Shorter production cycles for heavy parts.
● Has a shorter lead time than injection moulding.
What is compression moulding?
Compression moulding involves taking a rubber compound and making a pre-form that is in the same shape, but a slightly bigger version, of the end product. At Martin’s Rubber, we have various compression moulding machines, ranging from 5 tonnes up to a 500-tonne press, with a maximum of a 1 square metre press area and daylight.
The process of compression moulding starts by loading the shape and closing the mould, which is heated by the press platens. The excess rubber is then vented from the cavity, along with any air under the compression force of the press, then held closed by the press whilst the rubber is cured. Then, when the press is opened, the tool can be split and the part de-moulded.
The benefits of compression moulding include:
● Does not create much waste.
● Capacity to process stiff, higher durometer materials.
● More cost-effective than transfer or injection moulding.
● Most suitable for smaller quantities.
● Best option for products that require a long cure time.
● Ideal for parts with large cross-section.
Contact Martin’s Rubber today
To find out more about the rubber moulding techniques at Martin’s Rubber, and all our products and services, call one of our technical experts today on 023 8022 6330 or email us at [email protected].
The post A guide to Martin’s Rubber’s rubber moulding techniques appeared first on Martin’s Rubber Company.