Why choose rubber injection moulding?
Posted on 18/01/2016 Category: Injection moulding
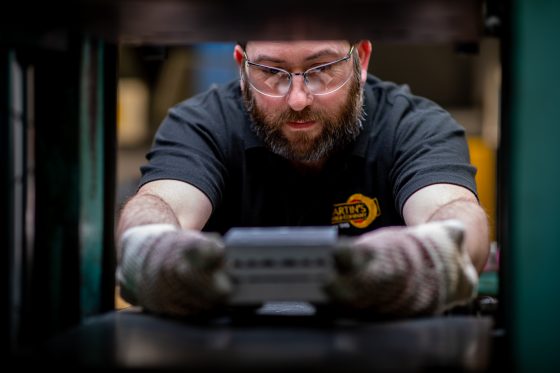
Take a quick look around your home, office or car and you’ll no doubt find countless products and parts that have been injection moulded. Our rubber injection moulding machines give us the freedom and flexibility to produce a broad range of parts quickly and competitively. Here, we give you an in-depth guide to our rubber moulding process, which is suitable for numerous grades of rubber materials. Rubber injection moulding is one of the most widely used manufacturing processes used in our industry today. Let’s take a closer look at the advantages of our rubber injection moulding process, as well as how it works in practice.
What is injection moulding for rubber?
Injection moulding is a manufacturing process used for producing parts by injecting material into a closed mould. Injection moulding can be performed with a host of materials, including metals, plastics, glasses and – in our case – thermoset elastomers and polymers. Parts to be injection moulded must be carefully designed to facilitate the rubber moulding process. The material used for the part, the desired shape and features of the part, the material and design of the mould, and the properties of the moulding machine must all be taken into account. It is essential to consider the quantity of parts required and the life of the tooling. This is because injection tooling and presses are more complex and require a larger volume of material; they are therefore more expensive to set up and run, than other rubber moulding techniques. Therefore, small batches of parts may not be cost-effective if manufactured by rubber injection moulding.
How does rubber injection moulding work?
Material for the part is fed into a heated barrel, mixed, and forced into a mould cavity, where it cures and hardens to the configuration of the cavity. Moulds are typically made from metal, usually either steel or aluminium, and precision-machined to form the features of the part. They may need to split in a variety of ways to eject the finished part, or locate inserts that are bonded into the product. Most elastomeric thermoset polymers can be injection moulded, although custom compounding may be required in order to facilitate the process. Since 1995, looking across the entire range of thermoplastics, resins and thermoset types, the total number of available materials for injection moulding has increased dramatically at a rate of 750 per year. There were already approximately 18,000 materials available when that trend began, and rubber injection moulding remains one of the most useful industrial processes ever invented.
Advantages of rubber injection moulding
● Fast production.
● Low labour costs.
● Design flexibility.
● High-output production.
● Multiple materials can be used at the same time.
● Can be used to produce very small parts.
● Leaves little post-production scrap.
● Ability to include inserts.
● Good colour control.
● Good product consistency.
● Reduced requirements for finishing.
● Good dimensional control.
● Disadvantages of injection moulding.
● High initial tooling and machinery cost.
● Part design restrictions.
● Small runs of parts can be costly.
One thing is for certain, Martin’s Rubber can give you all the advantages of injection moulded rubber products with none of the disadvantages. Contact us today on 023 8022 6330, or email [email protected], for more information about all our rubber manufacturing services and products.
The post Why choose rubber injection moulding appeared first on Martin’s Rubber Company.