A guide to rubber recycling
Posted on 20/03/2020 Category: Rubber Recycling
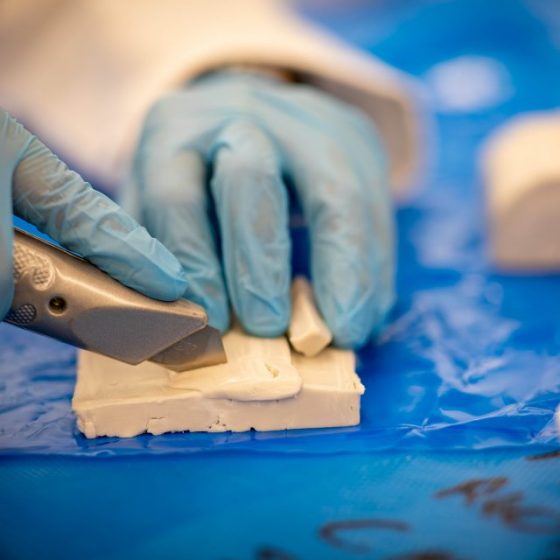
Martin’s Rubber is always seeking new solutions to pressing industrial challenges. In our increasingly environmentally conscious society, the issue of single-use plastic has quite rightly gone under the microscope. As rubber engineering experts, we are only too aware of the impact of rubber products going into landfill. The environmental impact of our industry’s output has driven us to develop our fully sustainable – and unique – Remould™ rubber recycling process, which enables us to break down and re-vulcanise nitrile rubber into brand-new Envirolast™ compounds for re-moulding.
Rubber recycling process
Rubber is difficult to recycle. Unlike plastic, you cannot simply heat and re-use rubber. Whereas thermoplastic materials can be heated, deformed and reprocessed into new or different products, the vulcanisation process permanently “sets” the bonds of a thermoset rubber. That process is hard to undo.
Think of rubber-like a sponge cake (bear with us!). When the cake has been baked, it’s impossible to extract the eggs to be re-used in another recipe. That, in a nutshell (or should that be eggshell?!), sums up the challenge we face when attempting to recycle vulcanised rubber.
It’s challenging, but not impossible, as Martin’s Rubber has proven.
Rubber recycling solutions
Alongside our industrial and academic partners, Martin’s Rubber has successfully developed a scalable, proprietary rubber recycling solution, known as Remould™. For the first time, this innovative process enables us to break down some of those aforementioned molecular bonds to produce a reusable material.
Remould™ technology creates a closed-loop recycling process that allows us to de-vulcanise end-of-life rubber products and re-vulcanise them into fresh ones. We simply combine the de-vulcanised rubber with a raw, virgin rubber compound to form new bonds and produce a newly moulded product.
This is how we make all of our sustainable Envirolast™ rubber products, which are kinder to the environment and just as uncompromising on quality as all our other rubber products. Martin’s Rubber is re-shaping the rubber recycling process, and you can be a part of this exciting revolution by choosing our Envirolast™ compound for your rubber products.
How does Remould™ work?
All of our products manufactured from Envirolast™ exhibit reliable, repeatable physical properties, as well as a high-quality finish. Currently available in nitrile, we can guarantee that up to 50% of the rubber in every product we mould from Envirolast™ has used recycled rubber from our game-changing Remould™ process.
Here’s a simple step-by-step guide to how the Remould™ process works in practice:
- • Step 1: We grind down the selected polymer into a consistent crumb, which is still vulcanised at this stage.
• Step 2: It is carefully blended with chemical “bullets” that facilitate the disconnecting of the crosslinks.
• Step 3: A degree of mastication, temperature and pressure is imparted to disconnect the crosslinks and reduce the rubber crumb into a fine, friable and fully reactive material.
• Step 4: It is then mixed with virgin compounds of the same polymer for moulding into new products.
Following this four-step Remould™ process, the original thermoset rubber can be incorporated into a new rubber compound formulation to be vulcanised and crosslinked into a functional product. Sustainable rubber recycling in the UK has arrived and Martin’s Rubber and is redefining our relationship with rubber for the better.
For more information about our Envirolast™ materials or the Remould™ rubber recycling process behind them, please contact Martin’s Rubber today on +44 (0) 23 8022 6330 or email [email protected].