What is the process of moulding rubber parts?
Posted on 22/06/2020 Category: Rubber moulding
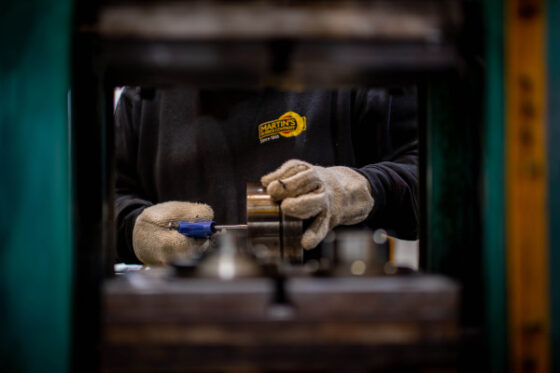
Rubber moulding is the process by which usable rubber products are manufactured from elastomers. This moulding process takes raw rubber compound which is placed into a mould and put under pressure at a high temperature to vulcanise. Martin’s Rubber has over 150-years of manufacturing experience in solving problems using rubber technology.
We have the material experts, toolmaking knowledge, rubber moulding experience, manufacturing skills and test equipment on-site. With all this at our fingertips, we can create moulded rubber solutions through rubber injection moulding or rubber compression moulding techniques.
What parts do Martin’s Rubber manufacture with rubber moulding techniques?
Martin’s Rubber has the capability and expertise to manufacture just about any product in rubber, including both rubbers moulded gaskets and rubber moulded seals.
A gasket is a mechanical seal between distinct substrate sections. This might be to seal a liquid or a gas or to provide additional benefits such as thermal or electrical insulation or conductivity. We have the expertise to design and manufacture rubber moulded gaskets suitable for any application within our size capabilities.
Rubber seals are used to prevent two elements from coming apart or to prevent anything from passing between them. We offer a range of fluid power sealing solutions here at Martin’s Rubber, including rubber moulded seals, and we also offer the option to prototype a seal by machining it in engineering plastic and taking it to a moulded option once tested and proven. With so many manufacturing and material options available, we can provide a technical solution to meet any requirement.
Rubber Injection Moulding
The rubber injection moulding process includes forcing a rubber compound into the mould cavity under high pressure. We recommend rubber injection moulding as one of the most efficient and repeatable ways of creating moulded rubber products.
The practice of rubber injection moulding started in the mid-1960s, following on from the process used to mould plastics and it works by heating the rubber and placing it under significant pressure to form a rubber part within a mould cavity.
To start with, the uncured rubber material is fed into an injection barrel, which is then warmed by an auger screw in a temperature-controlled barrel. The rubber material is then injected into the mould cavities by an injection press, with the auger screw turning to refill the injection barrel when the material is cured in the heated mould. The newly moulded part can be removed once the mould opens, and the injection press is ready to mould another part.
What are the advantages of rubber injection moulding?
The process of rubber injection moulding has a number of distinct advantages, these include:
- Reduction in material wastage
- Faster production process leading to larger production volumes
- Reduction in labour costs
- Consistent and repeatable parts.
What are the disadvantages of rubber injection moulding?
Whilst rubber injection moulding does have its fair share of advantages, there are also a number of disadvantages to the rubber injection moulding method. These include;
- The initial cost of tooling can be quite high due to the complexity and the number of cavities
- The process is only suitable for relatively high-volume production runs due to the amount of material required and the outlay in tooling costs.
Rubber Compression Moulding
Rubber compression moulding is the simplest form of rubber moulding. The rubber material is placed in a mould cavity directly, and it takes the shape of the cavity once the mould is closed and placed under pressure and heat. Rubber compression moulds differ in size and shape and can produce a variety of moulded parts.
Compression moulding is often chosen for compounds that have a medium hardness and is perfect for low-volume applications or in applications that require particularly expensive materials or complex designs. The compression moulding technique helps to minimise the amount of overflow and waste created by the rubber moulding process id designed correctly.
What is the rubber compression moulding process?
Uncured rubber is placed in the mould and then closed under hydraulic pressure and heat. The part is removed once the mould opens up, and any excess rubber is trimmed from the part to create the correct shape for the moulded rubber part.
What are the advantages of rubber compression moulding?
Rubber compression moulding is well suited to smaller production volumes, or with a requirement to manufacture large parts. The lower tooling costs means that rubber moulding via compression moulding techniques is a cost-effective solution for rubber manufacturing.
What are the disadvantages of rubber compression moulding?
Clear disadvantages of rubber compression moulding can also be seen. These include higher wastage of material from overspill and a slower processing time overall per part.
Martin’s Rubber have the expertise to create rubber that suits a range of applications and scenarios, including:
- Filling an awkward gap in an application
- Reducing noise or vibrations
- Meeting the requirements of extreme environmental performance
- Meeting the needs of insulative or conductive performance
- Creating materials that shield for RFI or radiation
- Meeting the needs of permeability or complete isolation
- Colour matching
- To meet the requirements and standards of your industry
- To test product designs prior to general manufacture
- To meet a deadline that you have been told is impossible
- To design and prototype, a product that you’ve been told can’t be made
- To satisfy the needs of a particular finish or aesthetic focus.
With over 150-years of successful rubber moulding and manufacturing, we have some of the most highly skilled rubber moulding industry experts working with us. The equipment we use is integrated with cutting-edge software, whilst our innovation in research techniques and material development ensures we always deliver incredible results and the best product to suit your application.
Speak to a member of our expert team to find out more about how Martin’s Rubber can create excellent quality rubber moulded products, specifically tailored to your requirements. Call our team on +44 (0)23 8022 6330 or email [email protected].