Troubleshooting guide to rubber injection moulding
Posted on 06/04/2020 Category: General Martins Rubber blog, Rubber moulding
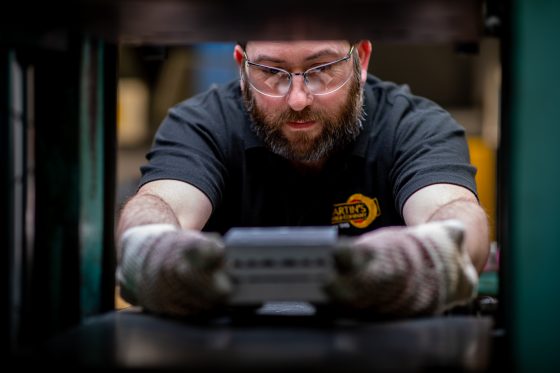
Rubber injection moulding is one of the most efficient ways to manufacture moulded rubber parts. Injection moulding rubber offers the combined advantages of lower unit costs, faster cycle times and high dimensional tolerances. Read on for our complete troubleshooting guide.
What is rubber injection moulding?
This particular type of rubber moulding process was created as an extension of the plastics industry in the 1960s. After overcoming initial issues relating to temperature (plastic is cooled during moulding whereas rubber is heated) and pressure (rubber injection moulding requires significantly more pressure per square inch of cavity surface), the process has become one of the most efficient ways to produce moulded rubber components.
Advantages of injection moulding rubber
Injection moulding rubber is an ideal process for high volumes of small to medium size parts, large shot weights, achieving close dimensional tolerances, and making components that require consistency of colour or total uniformity.
Quality control when injection moulding rubber
Quality control is a major part of the rubber moulding process. The vast majority of quality control issues arise as a direct consequence of equipment, material and process conditions. Some studies suggest that around 60% of defects are due to equipment, 20% from moulds and dies, 10% from the material, and a further 10% from operator error.
Typical problems with injection moulded rubber (and solutions!)
There are countless quality control issues that can arise from manufacturing injection moulded rubber. Here are five common problems and possible solutions. Of course, the best way to ensure a positive outcome with your moulded rubber is to employ an expert, like Martin’s Rubber!
1. Short Shot
A short shot is the incomplete filling of a mould cavity, resulting in an incomplete injection moulded rubber part. There are several possible solutions to remedy short shot issues.
Possible solutions:
- Increase shot size
- Use higher melt flow rate material
- Increase melt or mould temperature
- Increase fill speed, pack pressure or injection time
2. Shrinkage
A common problem when manufacturing rubber products is the fact that moulded rubber parts always come out of the mould smaller than the cavity that produced them. In other words, they shrink.
Possible solutions:
- Maintain adequate cushion
- Delay gate sealing to allow pack out
- Increase the size of the mould cavity
- Increase cavity pressure and hold time
3. Excess flashing
With injection moulding, the rubber material can leak between the mould’s surfaces along the parting line. Flashing can affect an injection moulded rubber part’s surface finish and sealing capabilities.
Possible solutions:
- Use a larger press
- Increase clamp force
- Decrease peak cavity pressure
4. Warpage
Warpage is when the intended shape of the moulded rubber part becomes distorted during the cooling process, which can cause it to fold, twist, bend or bow.
Possible solutions:
- Increase cycle time
- Decrease injection fill rate
- Minimise hot spots in the mould
- Mould at high temperatures and low pressures
5. Brittleness
Brittleness can result from shorter molecular chain lengths. This impairs the physical integrity of an injection moulded rubber part, resulting in cracks or breakages.
Possible solutions:
- Increase injection fill rate
- Increase mould temperature and cool time
- Eliminate contamination from other polymers
For flawless rubber injection moulding results, contact Martin’s Rubber today on +44 (0) 23 8022 6330 or email [email protected].