The process of rubber prototyping at Martin’s Rubber
Posted on 15/03/2019 Category: Rubber Industry News, Rubber moulding, Rubber sheeting
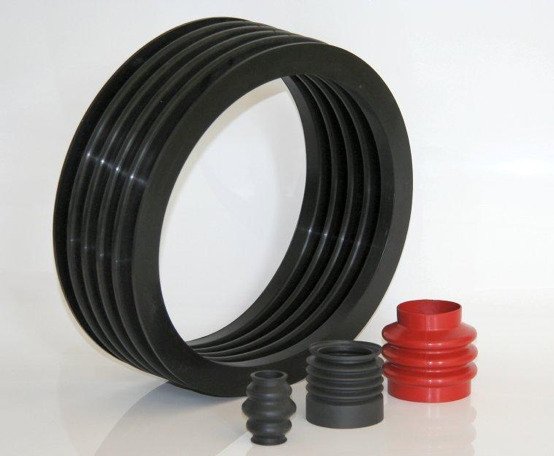
If you’ve ever wondered how to make a rubber prototype, Martin’s Rubber can reveal all. With a combination of collaborative working, dynamic CAD modelling and in-house tooling, we can produce realistic rubber prototypes in double quick time. Here, Martin’s Rubber details the wealth of expertise that goes into producing every one of our rubber prototypes.
American automobile magnate and manufacturer Henry Ford rolled out nearly as many great catchphrases as he did vehicles over the course of his lifetime. One of our favourites is this particular nugget: “Coming together is a beginning, staying together is progress, and working together is success.” For us, this mantra really encapsulates the value of collaboration.
When it comes to developing a new rubber part or product, seeking out the wealth of experience and expertise on offer here at Martin’s Rubber is the best first step you can take. Working with us over the course of the design and production processes is a sure-fire way to accelerate the progress of your desired rubber product and ultimately achieve your operational goals and aspirations.
More often than not, this collaborative approach begins with a prototype.
How to make a rubber prototype
Once we have received your drawing, sample or CAD model and have discussed your application requirements in detail, our experts can then recommend suitable materials and design characteristics to develop a product that will most closely meet your expectations. We can then use dynamic modelling software, called finite element analysis, to test the integrity and performance of a design by simulating the stresses involved in your application.
This virtual prototype helps to inform the resulting physical prototype, providing a relatively low-cost, low-risk solution that eradicates trial and error. This naturally streamlines and speeds up the process of bringing your product to production. Before we reach the manufacturing stage, you will likely want to see and touch a physical prototype that provides a tangible idea of what the finished product will look like.
This is where our in-house tooling department comes in.
In-house tooling for rubber prototyping
Martin’s Rubber has had a tooling department on-site since the 1940s. We realised early on that having our own dedicated tooling expertise gives us the ability to be agile, responsive and innovative. Using cutting edge CAD and CAM software, we can import your 2D or 3D drawings to design an appropriate mould tool capable of producing your desired part. This gives us the advantages of being able to work collaboratively with you and, pending your approval, producing a prototype extremely efficiently.
Where time is of the essence, we can even supply a rapidly prototyped part for approval. We can use rapid machining techniques – such as 5-axis CNC machining, spark erosion and surface grinding – to develop a pre-production part using your exact design parameters and material specifications. This provides a real-world impression of exactly how your part will look, feel and perform. We are also exploring innovative 3D printing techniques for the rapid manufacture of parts using real rubber.
Let Martin’s Rubber develop your rubber prototype
Martin’s Rubber has more than 150 years’ experience in developing first-class elastomer products. Our exemplary in-house facilities, as well as the scope of materials and techniques that we offer, allow us to be responsive and innovative – not least in the production of bespoke prototype parts. We strive to build working partnerships with our customers and are passionate advocates for British engineering and manufacturing.
If you’d like to find out more about how to make a rubber prototype, please contact Martin’s Rubber on +44 (0) 23 8022 6330 or email [email protected].