What types of rubber testing are there?
Posted on 26/06/2020 Category: Rubber Testing
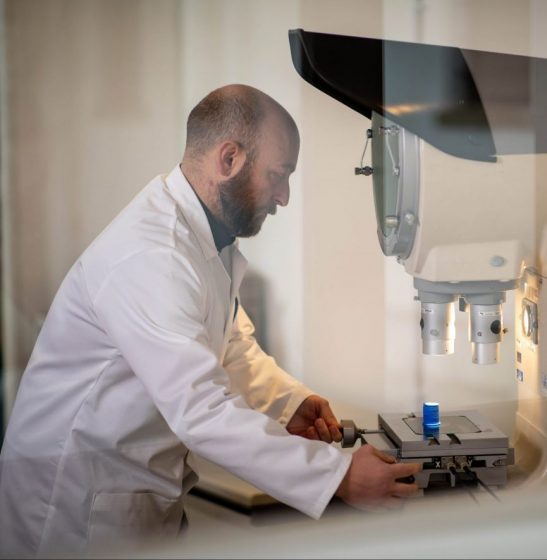
At Martin’s Rubber, we pride ourselves on manufacturing the highest quality rubber components and sealants. Whether at our own facilities or a partner testing house, where required, we can rigorously test every product before it reaches our customer. In this article, we highlight three major types of rubber testing that we use to maintain our high standards.
Finite element analysis
Finite element analysis, or FEA for short, is a rubber testing technique that uses computer modelling technology to predict how a rubber product will respond to stress and strain. This innovative approach provides us with critical data that our experts can interpret to ascertain whether a specific design will perform optimally according to an application’s specific parameters, allowing us to work with customers to adjust a design prior to reaching manufacture stage.
As you can imagine, FEA has become an invaluable tool. With finite element analysis rubber testing, we can take some of the time and cost out of the development and prototyping phase. Our highly accurate modelling software enables us to make informed decisions about material selection to eradicate costly product failures at the design stage. This is a hugely exciting development, which allows us to manufacture durable rubber parts with incredible accuracy.
Moving Die Rheometer (MDR)
A Moving Die Rheometer, or MDR, is a piece of rubber testing equipment that we use to assess the viscosity and elasticity (viscoelasticity) of rubber compounds. We can do this before, during and after the curing process. This type of rubber testing allows us to check whether the raw material is performing within set parameters for us to then confidently produce repeatable, consistently high-quality products.
With this standardised rubber testing technique at our disposal, our technical experts here at Martin’s Rubber can take full control of the manufacturing process. Time and time again, the data we are able to extrapolate from an MDR allows us to maintain the highest standards of quality and process control during the manufacturing of products. In fact, this is one of the go-to types of rubber testing we employ when producing new materials in research and development projects.
Rubber fatigue testing
Rubber fatigue is a gradual process that eventually weakens and impairs the performance of a rubber component. As you can imagine, rubber fatigue can have dire consequences. Were it to impede the efficient running of plant machinery, at best it might halt productivity and at worst it could injure personnel. For those reasons, rubber fatigue testing is essential for manufacturers that routinely work in hazardous conditions.
Fatigue testing equipment allows us to replicate the parameters of a specific industry application to put the rubber in question through its paces. This method of rubber testing puts an appropriate strain on the rubber to facilitate crack growth and nucleation. Fatigue testing machines are incredibly accurate, which enables us to provide our customers with a precise analysis of how a rubber component will perform before they purchase it.
Why choose rubber testing from Martin’s Rubber?
With more than 150 years of rubber engineering experience, Martin’s Rubber has a proven track-record of producing high-performance rubber parts for countless industries and applications. Whether you require a lightweight, heat resistant or high strength rubber part, our various types of rubber testing techniques allow us to design and manufacture the most reliable and durable rubber components available.
Find out how our rubber testing services can enhance your operations. Contact Martin’s Rubber on +44 (0) 23 8022 6330 or email [email protected] today.