What causes rubber to deteriorate?
Posted on 27/01/2020 Category: Rubber Testing
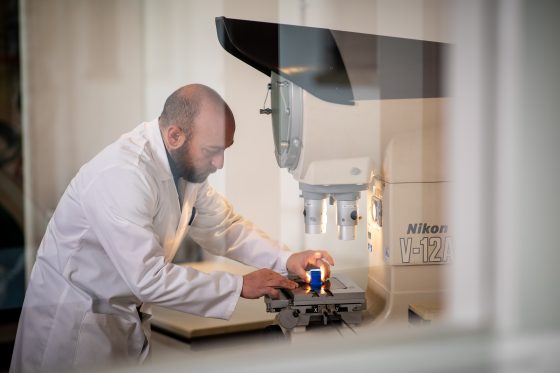
Rubber is a wonderfully useful and malleable material. Like most materials though, rubber degradation will eventually occur over time due to common environmental factors like heat, light and ozone. Naturally, this can impair the functionality of critical rubber parts, like seals and O-rings, and could lead to machine failure. Read on to find out more about typical rubber deterioration causes and practical ways to prevent rubber deterioration.
What is rubber deterioration?
Most elastomers undergo rubber degradation over time and the most common rubber deterioration causes are exposure to light, oxygen (ozone) and heat. The molecular changes brought about by these environmental conditions can significantly impact the mechanical properties and therefore service life of rubber products like seals and O-rings.
Oxidative and thermal ageing of rubber are accelerated by stress and reactive gases, like ozone, resulting in cracking, charring and colour fading. However, the addition of antioxidants, UV stabilisers and antiozonates can slow or prevent these types of issues.
Oxidative rubber degradation can cause hardening or softening, depending on the structure of the elastomer. Hardening is more common because free radicals produced due to heat, oxygen and light combine to form new crosslinks, which reduces the flexibility of the rubber.
How does rubber deteriorate?
As we touched upon briefly above, the two main forms of rubber degradation are: hardening (or embrittlement) and softening. From a molecular perspective, these chemical processes are known as “chain hardening” and “chain scission” respectively. The chemical makeup of the polymer will determine which type of deterioration will ultimately occur.
For instance, the polymer polybutadiene and its copolymer derivatives – such as styrene-butadiene-styrene (SBS) and nitrile rubber (NBR) – is developed using a process called cross-linking, which involves joining polymer chains together to form one single molecule. Free radicals produced by heat, oxygen and light combine to form new crosslinks, which reduces flexibility and leads to hardening. This is chain hardening.
Natural rubber (polyisoprene) and other isoprene polymers, on the other hand, are susceptible to chain scission. These types of rubber are developed using polymerisation, which entails bonding multiple identical molecules – or monomers – to form a polymer. As such, their polymer main chain is liable to degrade, which is the act of chain scission, and leads to the softening of the rubber material.
Some other polymers like EPDM can undergo crosslinking and chain scission. However, crosslinking reactions tend to dominate, leading to a greater likelihood of hardening over time.
How to stop rubber deterioration
Even before a rubber product is manufactured, a computer modelling technique known as finite element analysis (FEA) can be used to predict a rubber material’s response to stress-strain conditions. FEA stress analysis illustrates whether a proposed design will function to design specifications prior to manufacturing a mould tool. This can help to prevent rubber deterioration in the long-term and provide significant cost-savings.
Once you have taken delivery of your rubber products, they should generally be stored in cold, dark, dry and oxygen-free conditions to slow the effects of rubber degradation. If you have any rubber components, particularly rubber seals, that are beginning to show signs of deterioration, fear not. Damage or weathering need not necessarily spell the end of life for a rubber seal or product, which can be costly and sometimes difficult to replace.
With the right rubber restoring techniques, and a sufficient level of care and maintenance, rubber seals and certain polymer products can often be brought back from the brink of failure and restored to functionality. Follow these simple and practical how-to steps on how to stop rubber deterioration to restore your rubber seals to their former glory.
- Step 1: Prepare – Clear any debris and detritus from the rubber item that you intend to restore.
- Step 2: Clean – Scrub off excess dirt to prevent future wear and tear, then allow to dry thoroughly.
- Step 3: Condition – Apply an appropriate rubber conditioner (check the product information).
- Step 4: Buff – Buff off damaged areas of rubber using a file or Emery cloth and reapply conditioner.
Read our guide to restoring damaged or weathered seals for more details. For further information about choosing the right rubber material for your product and preventing rubber degradation, please contact Martin’s Rubber today on +44 (0) 23 8022 6330 or email [email protected].